Exploration with python in rhinoceros
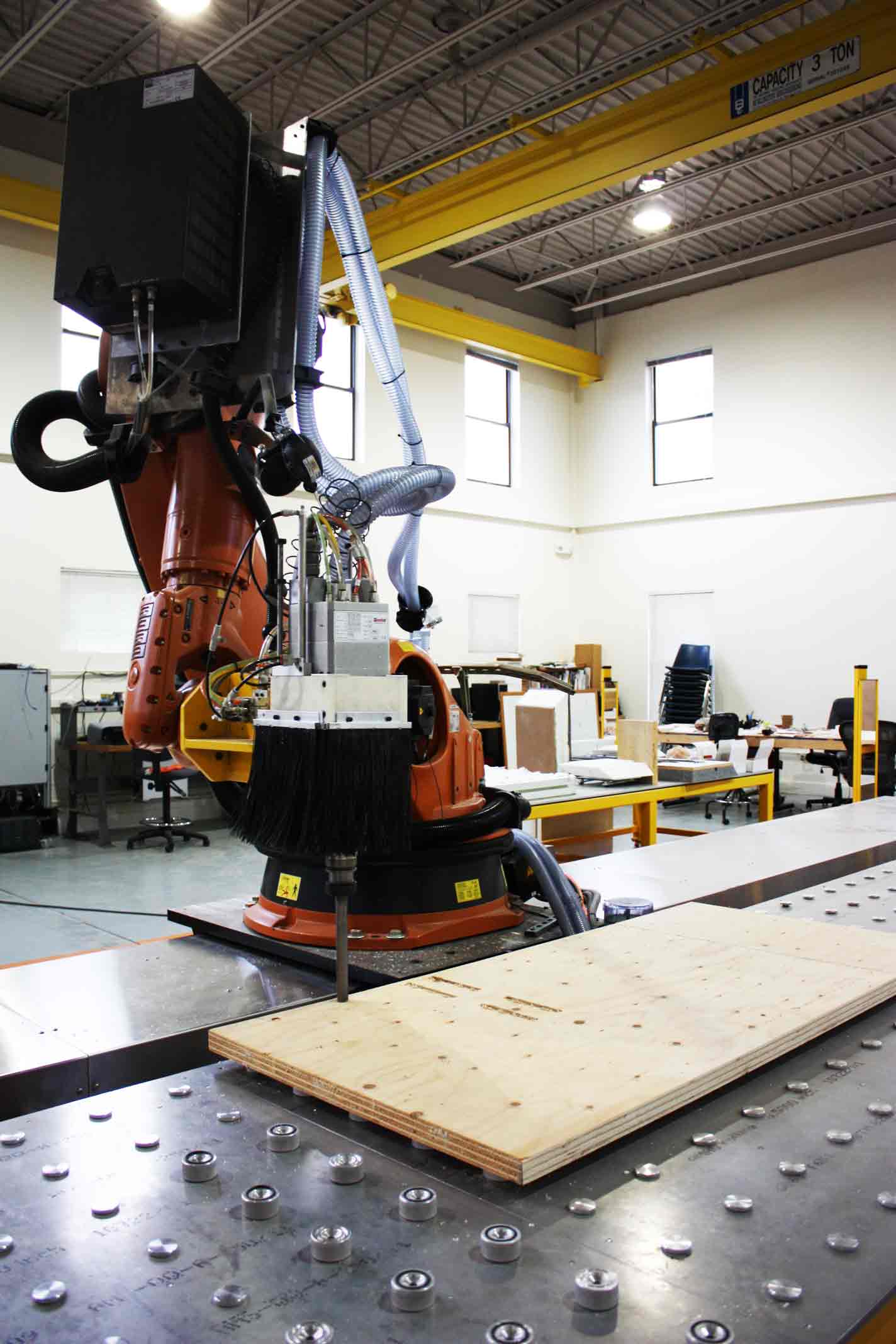
Milling with a robot is an unusual thing. Robots, in this case the KUKA robot, are largely used in the automotive industry where they usually do a single routine, a so-called job. Each robot executes a single job geometrically following a set of 3D-Curves (circular, linear or point to point movements), programmed to do the same operation for the whole lifecycle of the machine. Milling with a robot means to program prototypical tasks for different jobs, and is therefore a fairly new application for robots and not widely used in the industry. Our first step was to learn how to control the KUKA robot to try to understand the basic principles of motion programming. There are 3 basic principles for motion control:
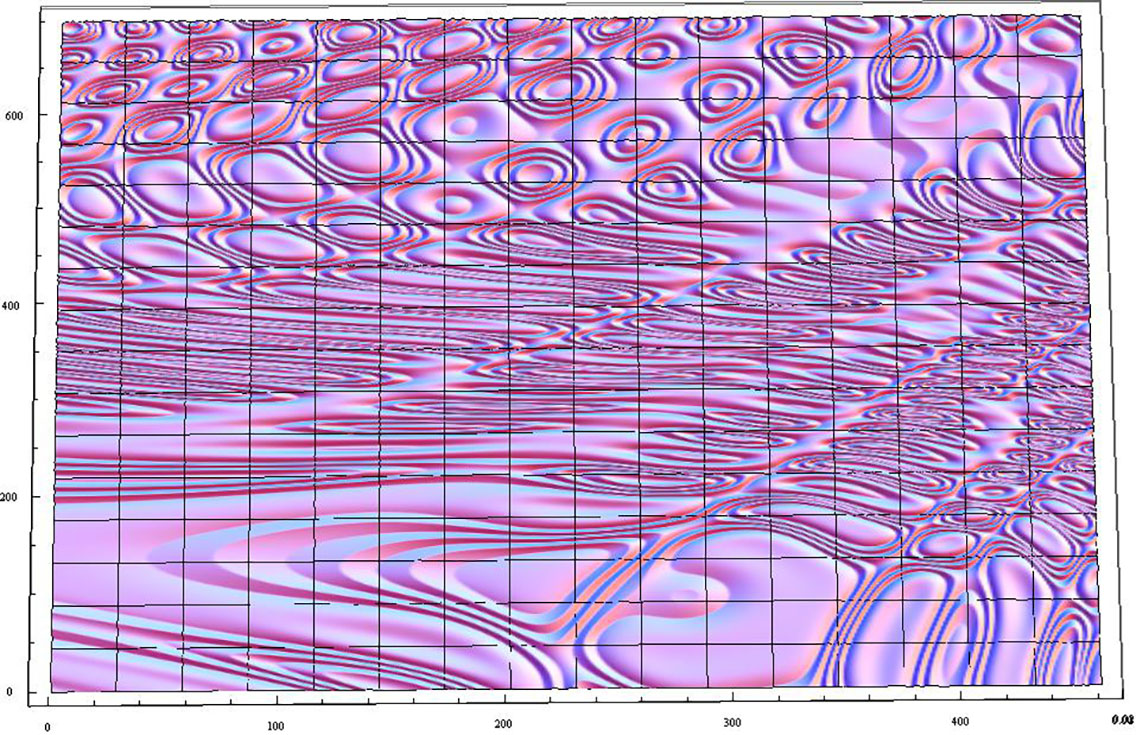
PTP ///// LIN ///// CIRC
In the PTP mode, the robot guides the TCP (in our case the spindle with the tool) along the fastest path, which is generally not the shortest path and is not a straight line. As the motions of the robot axes are rotational, curved paths can be executed faster than straight paths.
In the LIN mode, the robot guides the TCP at a defined velocity along a straight path to the end point.
For the CIRC mode, the TCP or work-piece reference point moves to the end along an arc. The path is defined using start, auxiliary and end points. The end point of a motion instruction serves as the start point for the subsequent motion.


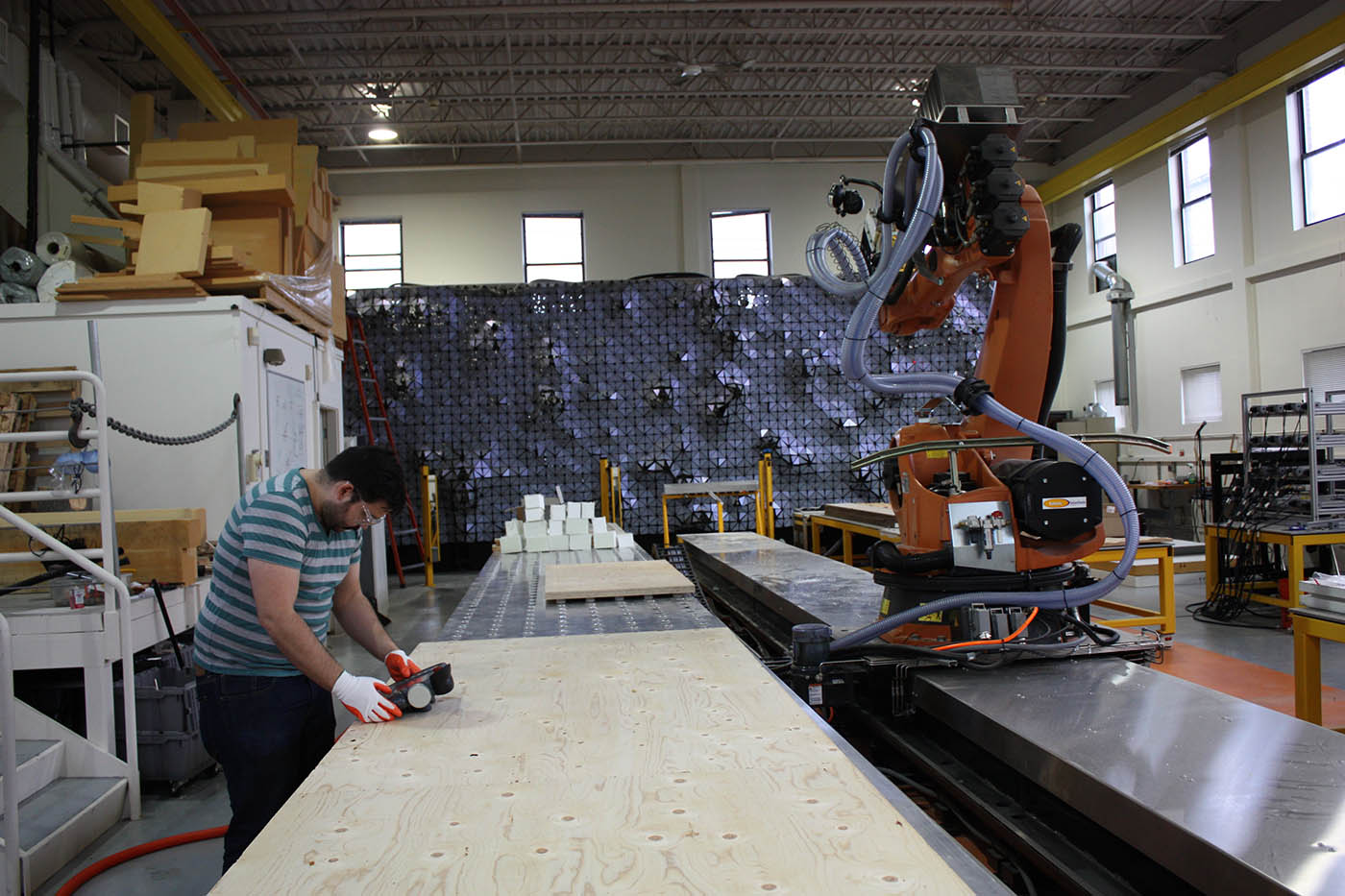